Hot Tap and Line Stop Fitting Designs
Proudly serving -> Industrial Service Companies, Oil and Gas Facilities, Power Generation Facilities, Nuclear Plants
We are the experts in hot tap design. We design fittings of all sorts, including, but not limited too:
Extruded split tee fittings
Fabricated split tee fittings
Extruded full encirclement saddles
Fabricated full encirclement saddles
Stub on fittings
Lateral hot tap fittings
Hot taps through blind flanges
Bag stop fittings
Completion flange designs
We design fittings to meet the following design codes:
ASME B31.3
ASME B31.4
ASME B31.1
ASME B31.8
ASME Section VIII Division 1
CSA Z662
API 653
Hot tapping does not have to be scary if you know what is needed to complete the work safely.
We assist from start to finish…
While we offer fitting designs, there is much more than just a fitting that makes a hot tapping job successful. We help you with the whole tapping project, including:
Project management
Live line welding analysis
Piping analysis
Custom support design
Alignment boss design
Fatigue analysis
Thermal analysis
Pressure testing
Finite element analysis
External pressure analysis
Hot tap machine load analysis
Weld burn-through analysis
What separates My Engineering from the competition is that we are involved in all steps of the hot tapping / line stopping process. We actively work with our customers and vendors to achieve the goal of safely, quickly, and effectively executing hot tap and line stopping projects.
Our clients involve us at the conceptualization phase so we can brainstorm potential solutions, identify safety risks, and assess the reason the hot tap or line stop is required. If a defect, process change, or process upset caused the need for a hot tap or line stop, we investigate the cause to ensure that the design solves the problem and takes into account all essential variables for safe and reliable operation of the piping system.
A few other things we do to ensure the hot tapping project is successful is:
We send early conceptual design concepts to our clients to gather feedback and perspective to ensure that no time is wasted in pursuing a solution that will not work for an unforeseen reason.
We work closely with manufacturing to ensure the design can be manufactured in the quickest amount of time, using available materials, and for the lowest cost.
Interested in learning more?
Having trouble understanding all the specifications involved in your hot tap project? Let us help!
Our engineers meticulously study all specifications to ensure all designs are fully compliant. We ensure each design is compliant with:
Jurisdictional requirements
End user specifications
Contractor quality programs and policies
Code requirements
Did you know that:
Suncor requires a finite element analysis for all reinforcing pad connections with a branch/run ratio exceeding 70%?
Shell does not permit reducing branch hot taps less than 1 NPS?
Transcanada Energy requires material testing (pull tests) on all fittings after postweld heat treatment / stress relieving?
If you need help with the specs, we are here for you.
Hot service? No problem
There are special requirements for hot service. You need to make sure that the cooling rate on the live line welding is appropriate to achieve the appropriate weld hardness.
You also need to make sure that you hydrotest with the appropriate test medium to prevent boiling. For very hot applications, a pneumatic test could be appropriate. We run all the stored energy calculations, safe working distance, and review the pneumatic test packages to ensure a seamless and safe pneumatic test.
Trust My Engineering with your hot tapping and line stopping designs to ensure your fittings are safe and effective.
Attention Albertans! Did you know it is possible to get split tees registered in Alberta?
We have the engineering knowledge to help you get split tee designs registered on pressure piping in Alberta.
Not from Alberta? Curious why ABSA considers split tees too risky to register? We can advise you on all the risks involved with split tee designs.
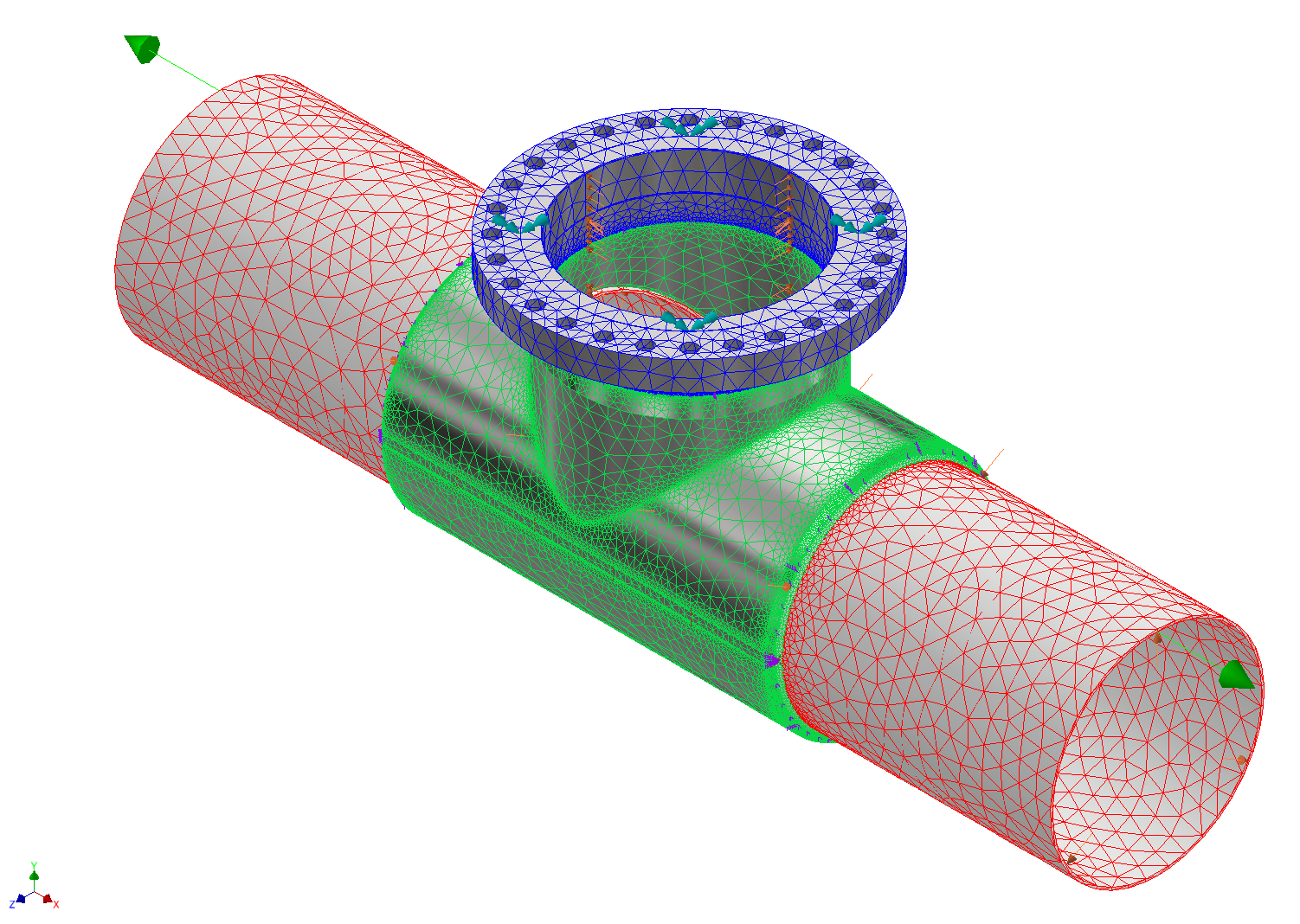
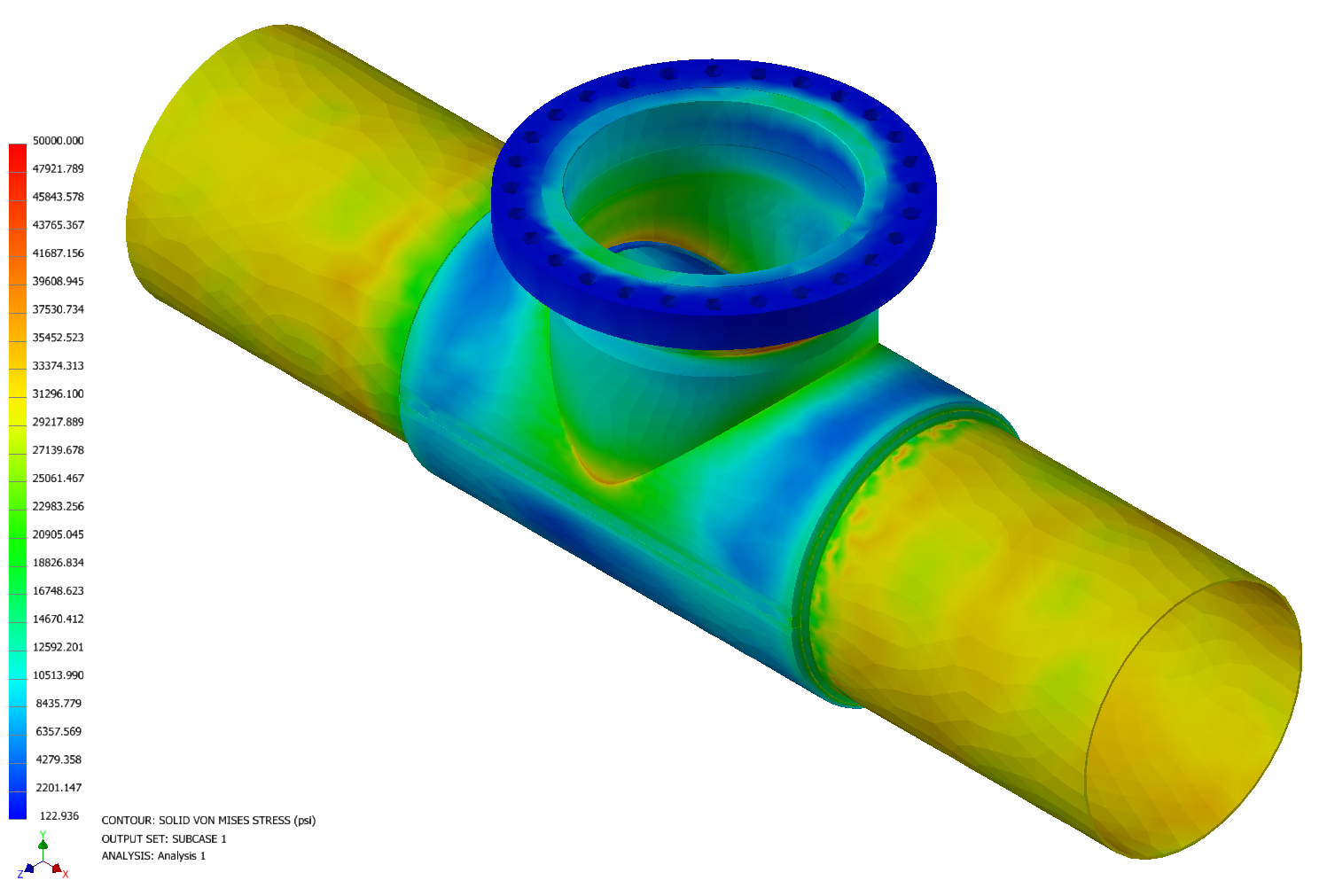
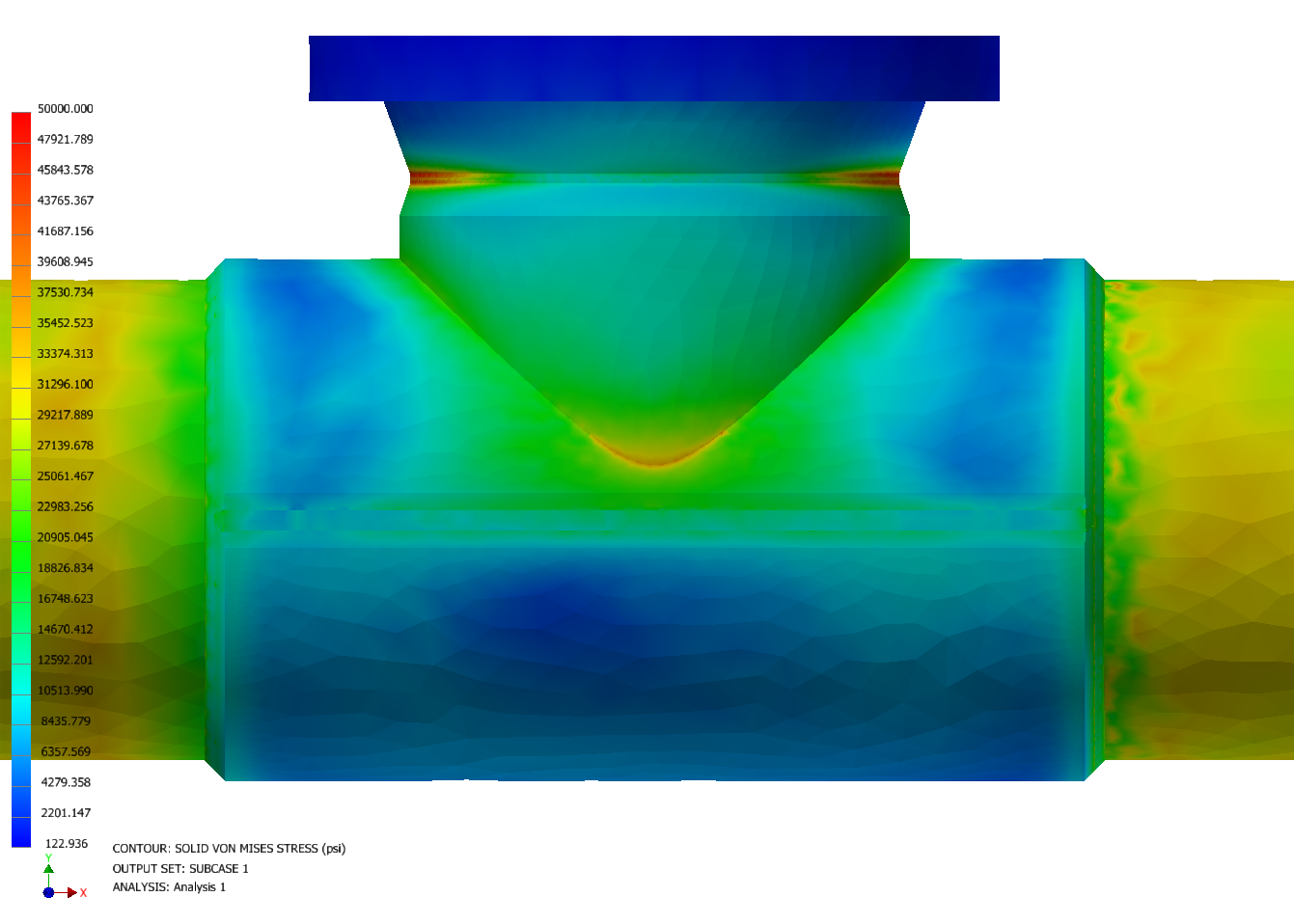
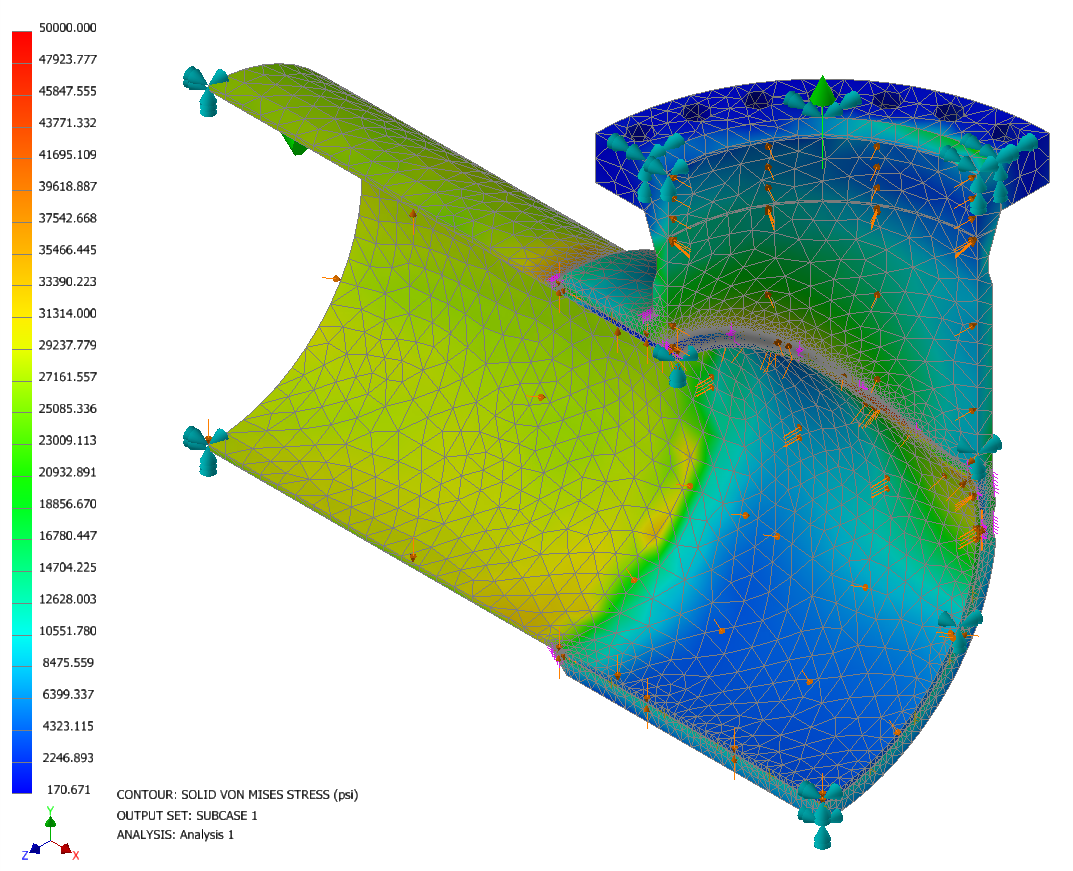
Get the best… everytime!
All designs from My Engineering include, at a minimum:
Machining notes
Stamping notes
Fitting weight
Pressure testing requirements
PWHT requirements
Customer / end user specific requirements